We would like to introduce the BCI Batch
control system. The system is designed to be highly informative, graphical and intuitive.
It is also very flexible in design and applicable to many different industries. This
version is PLC controlled with a small-form-factor PC HMI and 15 color touchscreen.
Below is a screenshot of the Main Screen. This screen will show all of the batch
information loaded from the recipe. Each step in the process will be highlighted and the
target information will be filled in during the batch.
The Batch ID is automatically sequenced for identification at the start of each run.
The batch below had been completed as indicated by the Mix Complete light and is in the
process of being bagged-out.
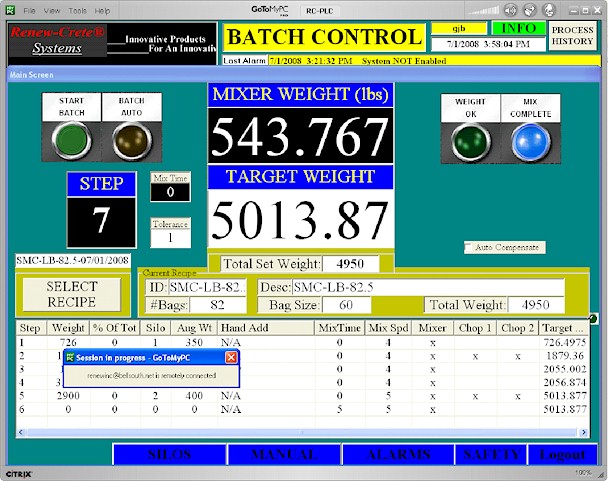
Below is a screenshot of the Recipe screen. The recipes are stored in an MSAccess database
that can either be on the local machine or network. MSAccess is not necessarily required
for this sytem.
Recipes are entered into the database with an easy to use form. You can enter batches by
Step Weight or by percent of total. You can enter total weight or number of bags and bag
size.
As you key in the recipe code on the touchscreen similar entries appear for quick
selection.
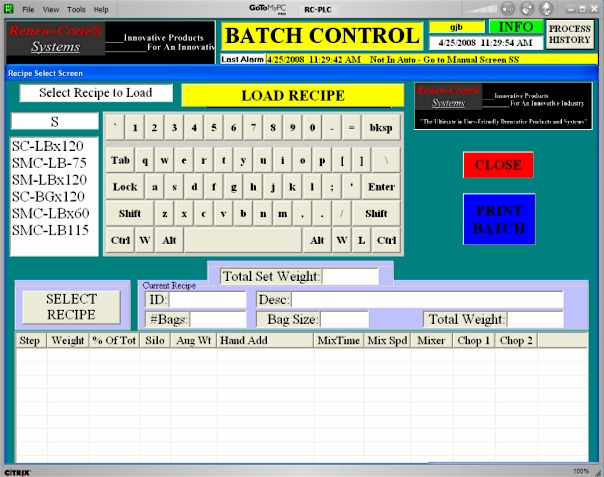
Once you have selected a recipe it is possible to print out a batch sheet to indicate the
type and amount of hand adds to pull and show the entire batch sequence. In this case it
prints out on a receipt printer.
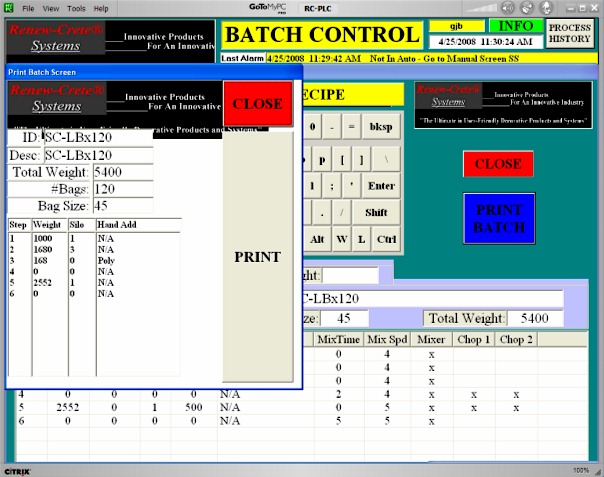
This is the manual control screen. The entire process can be commanded in manual mode here
and the status is reported with indicator lights. The main mixer drive speed is commanded
from a drop-down list. In this case, the VFD had preset speeds.
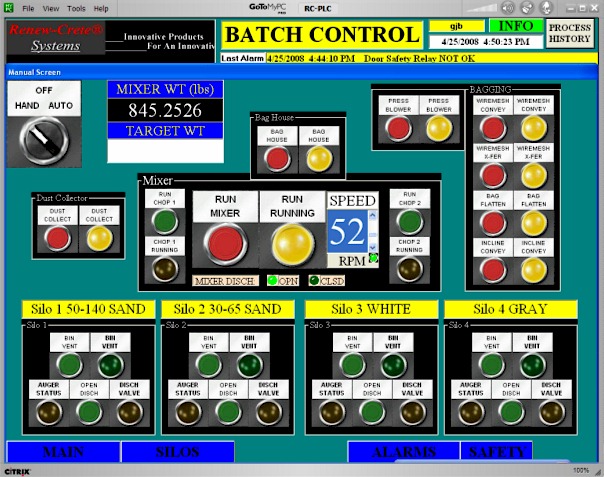
This is the Silo Overview screen. The status of each silo is reported by indicator lights
and a vertical bar graph is used to show an estimate of material remaining that is
continually updated after each step of each batch. Silo material weight can also be
entered manually. Alternately, silo level sensing can be provided. Here you can also
adjust the Freefall weight for each material. The Silo title header is variable.
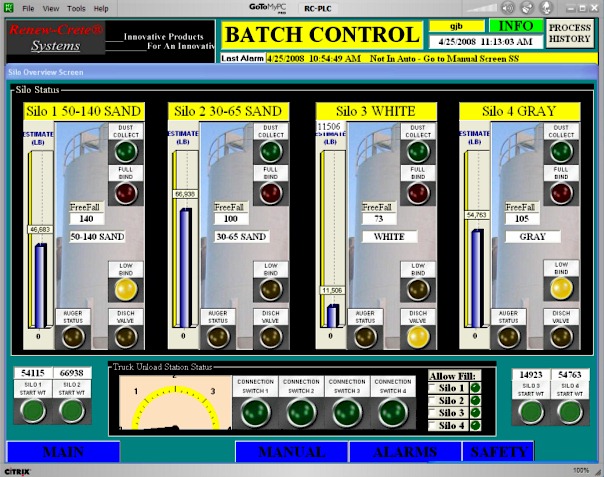
Additionally, the truck unload station includes error proofing to prevent selecting the
incorrect silo to fill. You can select which silos to be allowed to fill by touching check
boxes. The truck driver must select the correct silo on the selector switch outside and
must hook up to the correct fill line.
Here is the Safety Status screen. The electrical system includes two-channel safety relays
for each zone.
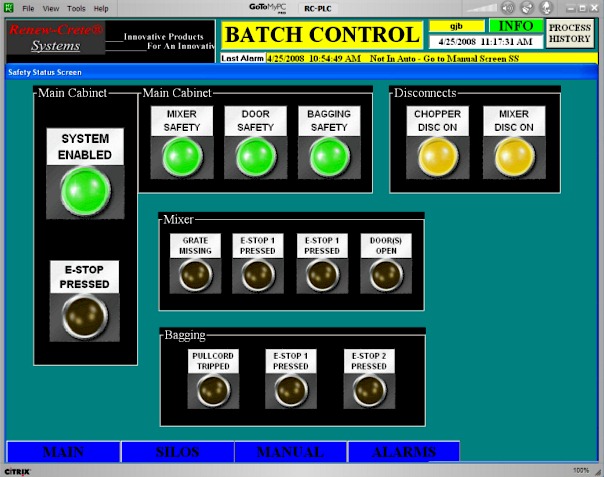
The system includes data collection of key variables. Each batch step is tracked. You can
search historical data by date, recipe ID operator or any combination. The data is stored
in the MSAccess database.
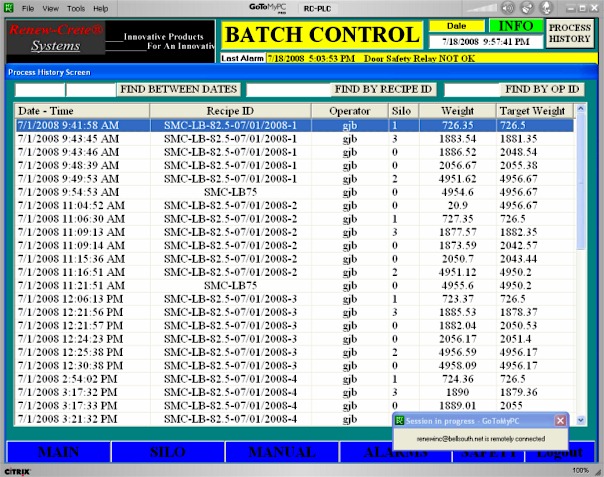
The system includes Alarm and Event reporting. The header area always shows the latest
alarm or event. Alarms are displayed with a red background, events are in yellow.
This is the Alarm History Screen. It is a scrollable list with all the alarms, showing the
latest on top.
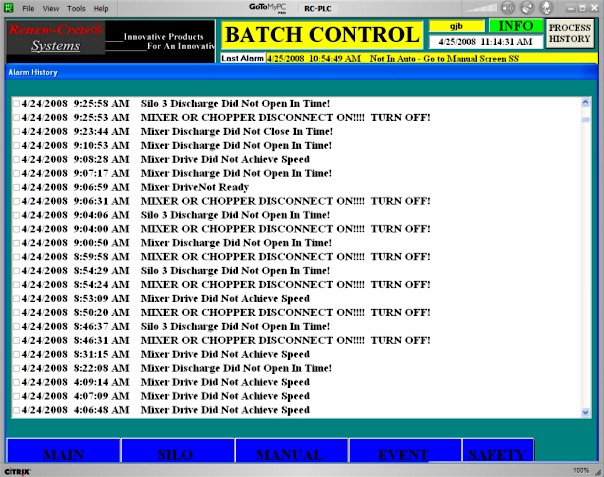
Below is the Event History Screen. Events are for operator info or to prompt operator
action
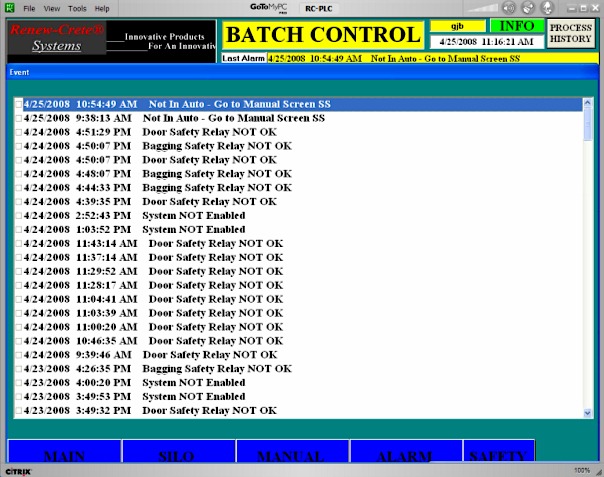
This is an example of how the main control panel might look. In this case the processor
was Allen Bradley CompactLogix with the latest DOL starter system on bus rails. The
15 Touchscreen was driven by a Stealth small form factor compuer
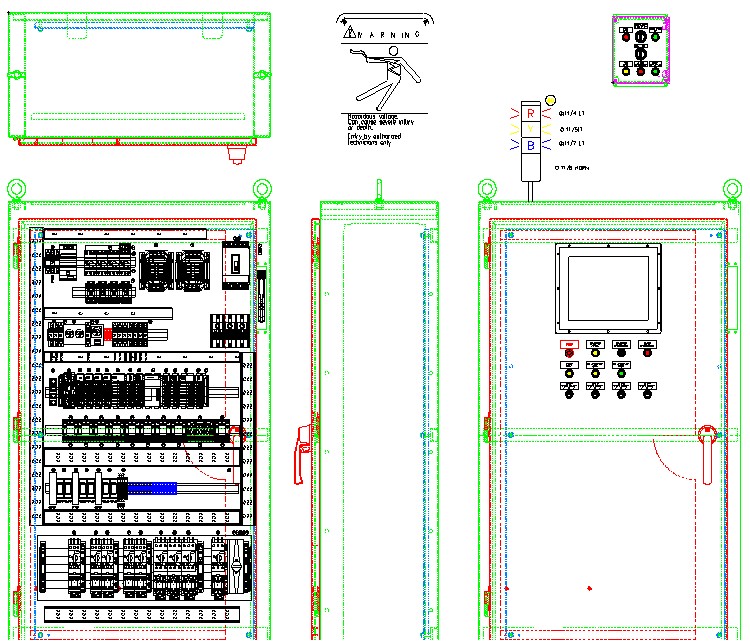
|